Our Engineering facts - busting myths and narratives
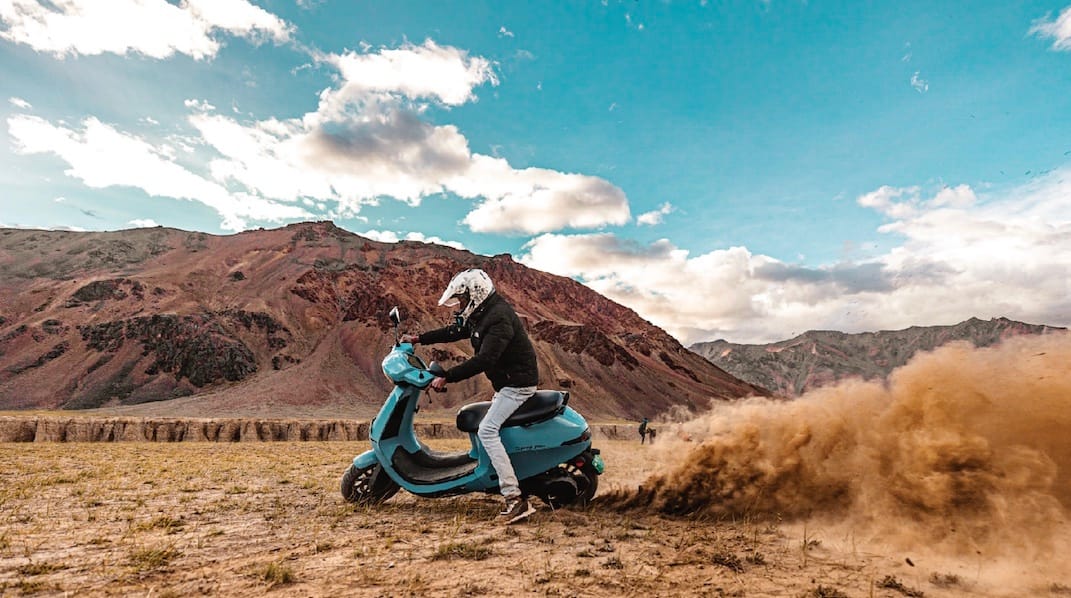
When we launched our products about 1.5 years ago, India’s 2W industry changed. We brought to market a world class product engineered and manufactured in India. And it has within a year become the best selling EV in India. And also one of the best selling scooters ever in India. For almost 100 years, there has been a template in automotive for product planning, manufacturing, how to sell to the customers etc. The OEM plans incremental products, gets technology from suppliers, assembles in house, and sells to dealers who sell to consumers. This is the reality that EVs and specifically Ola has disrupted. We make more than 50% of the value of our products in house, bring world class features to customers ahead of the curve, and have a direct relationship with our customers.
This reality has been hard for our detractors to live with and there’s been a non stop effort for the last 1.5 years to throw mud at us in one form or another. Over the last 2 days we’ve seen another such attempt. And I’m sure this won’t be the last. So for those who want to know the facts, we are publishing this technical blog about the engineering behind the Ola scooter, which will dispel many myths and bust many fake narratives.
In this blog, we will address the following points:
- The Engineering behind the Ola S1, including safety and testing we have undergone
- Deep dive into the specific front fork issue – the data, engineering, the misleading campaign and our continuous engineering improvement activities
- What process Ola followed for an upgrade. Also, what is a recall, when do automakers do it, and what process is followed
1. Engineering
We had acquired a European company called Etergo. It was already a world class scooter and rigorously tested under the stringent European standards but we have fully reengineered it to be the best suited for India. While a myth is being perpetuated that the vehicle has not been engineered and tested for India, the reality is completely different. We have gone through as rigorous a process of engineering, testing, validation and homologation as possible. The whole vehicle has been tested at 3 levels – digital simulations, component tests and vehicular lab tests, and vehicular field tests. We follow an industry leading product development and engineering process from concept development to virtual and physical development before deployment and production.
1.1 Digital testing: Extensive CAE simulations as a part of the virtual validation helps us ensure all adverse road and environment conditions are evaluated in a virtual environment before physically testing the vehicle. We are one of the most advanced OEMs in using digital tools and that enables us to bring products to market faster without compromising any quality.
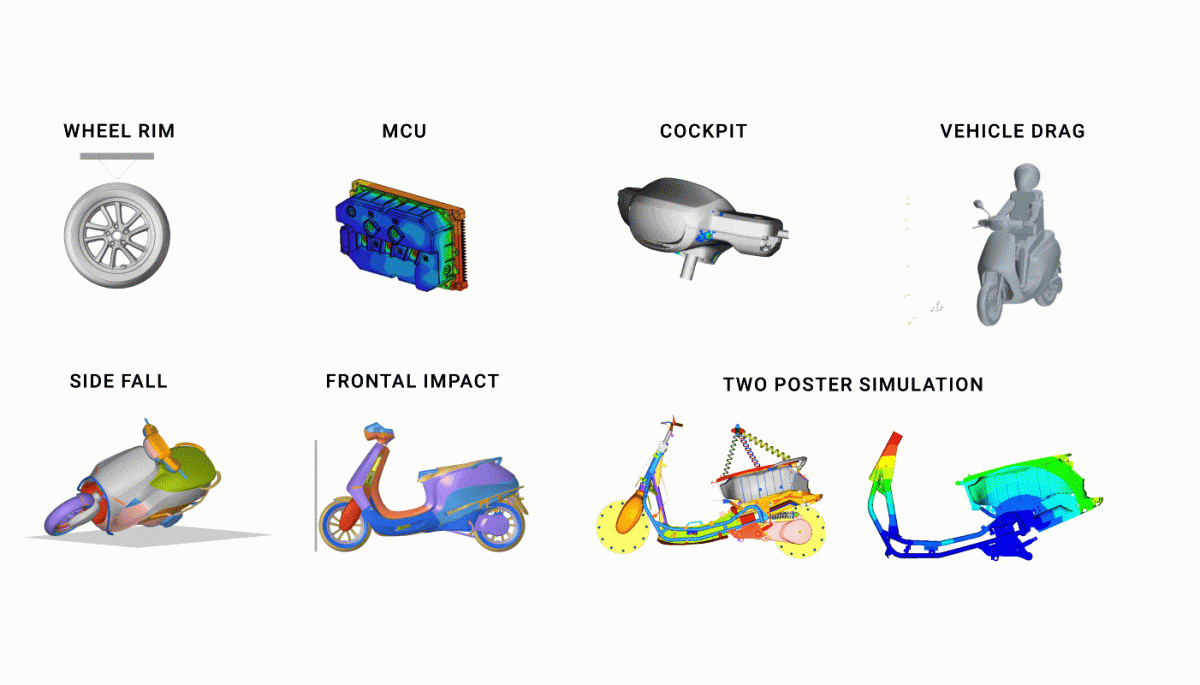
1.2 Component and vehicle testing in lab/controlled environments: To deliver the safest riding experience, we conduct a series of rigorous tests across components and vehicle level testing which pushes the vehicle to its absolute limits. We have tested 200+ components and 5000+ data points across functional, environmental, mechanical, structural, electrical and safety tests.
We have done all tests required by a 2W company and there are too many to list here.. But in addition, we have done all crash tests that hardly any 2W company would do, only 4W companies do. And we have done many tests in “Indian conditions” which again are to stress test the system for India and make sure it is the most rugged. Instead of enumerating each, here’s a video that shows our testing and validation efforts.
1.3 Real world vehicle testing: We have tested our vehicle for more than 4 Million Kms with 736 scooters, one of the highest and most rigorous testing standards in the industry. Our scooters have been tested by 500+ engineers and riders across the length and breadth of the country in temperatures as high as 50 degrees and as low as -10 degrees. Here are some images and videos.
2. Front fork
Now, let’s come to the front fork. Firstly, let’s look at the data. We have had 218 failures out of more than 2,00,000 vehicles on the road and more than 700 Mn kms driven. Out of these, 184 are accident cases. 34 are inconclusive or not accident linked. 34 out of 2,00,000 is 0.015% and 34 in 700 Mn kms is 1 in 20 Mn kms.That number is low enough by any automotive standard to not address. But we decided to address it head on. We saw the first inconclusive case in May 2022. We reengineered the front fork by August as part of our continuous engineering and improvement cycle, completed the tooling, testing and validation process by December and it was in production by January 2023. This pace of engineering is much faster than the conventional automotive world.
The original part by design has a 75% safety margin over and above compared to conventional twin fork systems. And with the new design, we made this margin 250%.
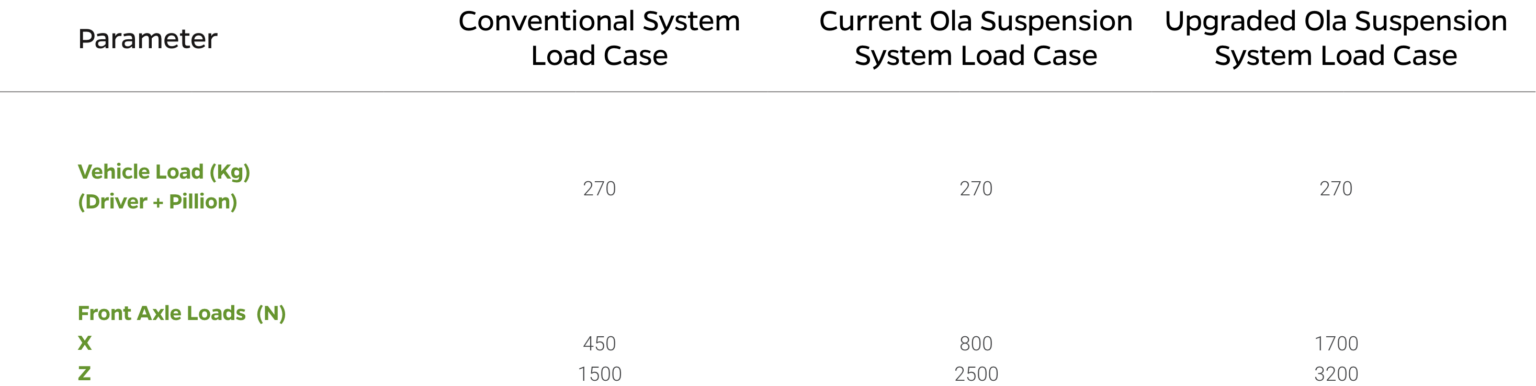
Stress Test

3. Our actions and upgrade
Through February and March, we’ve been facing a concerted campaign by publishing images of the front fork broken. Many of those images are the same repeated multiple times from different angles, and many are just accident images. Why is this attack only on us? Well, it’s obvious who the leader in EVs is and who is threatened by us.
This campaign against us was impacting some of our customers and we proactively decided to address our customer community and allow all of them to upgrade free of cost to the new design if they have any anxiety.Now let’s get into the recall process since many of you have been asking us about why it’s not a recall. Typically to order a recall, regulators mandate a ceiling of failures beyond which automakers are mandated to recall. In India that is 2% of all vehicles sold. OEMs sometimes do voluntary recalls at lower failure levels by observing the failed parts over a time horizon and concluding that there could be higher level of failures in the future.In our case, the failure rate is really low. No OEM at these failure levels will immediately call for a full recall. We would normally study the part for a longer lifespan and maybe decide after a few more months to see if the failure rate is rising and beyond an acceptable threshold. But instead, we have decided to allow all our customers to use the upgraded version if they feel more comfortable with that. The original part has not breached any safety limits by any OEM standards.We will always keep our customer interests first and will never deter from any amount of sustained campaigning against us. The EV revolution is truly on in India and it sure is making lots of people uncomfortable. Attacking Ola is not the way out. The more you attack us, the stronger India’s EV revolution will become!To conclude, let me leave this customer’s video with you – enjoying doing heavy duty stunts on his Ola S1 which uses the original fork design! Enjoy!!